
Comprehensive Guide to Wire Testing: Pull Testing, Torsion Tests, Fatigue Testing, and More
Understanding Wire Testing
Wire testing is a critical aspect of ensuring the reliability, safety, and performance of wires and cables used in various industries. It involves subjecting the wires to a series of controlled tests to assess their mechanical, electrical, and thermal properties. By understanding wire testing and its methodologies, manufacturers can make informed decisions about product design, materials, and applications.
Wire testing is facilitated by various types of testing machines, each with its own set of advantages and considerations. These machines are designed to apply controlled forces and stresses to wires, replicating real-world conditions to evaluate their behavior. Here's an overview of different types of testing machines commonly used:
Manual Testing Machines
These machines are operated manually by technicians. While they offer a hands-on approach and can be cost-effective, manual testing machines might have limitations in terms of precision, repeatability, and operator-dependent variations.
Automatic Testing Machines
Automated machines are equipped with advanced features and computerized control systems. They offer higher precision, accuracy, and repeatability compared to manual machines. Automatic machines are suitable for high-volume testing and tasks that demand consistent results.
Universal Testing Machines
These versatile machines are capable of performing various types of tests, including tension, compression, bending, and torsion. Universal testing machines are suitable for comprehensive wire testing, allowing manufacturers to assess multiple properties using a single device.
What is Wire Testing and Why is it Important?
Wire testing is the process of evaluating the mechanical properties and performance of wires used in various industries. It involves subjecting wires to different tests to measure their strength, durability, and reliability. Wire testing is essential to ensure that wires meet the required standards and can withstand the intended applications.
Pull Testing for Wire Strength
Pull testing, also known as tensile testing, is a common method used to evaluate the strength and load-carrying capacity of wires. It involves applying a pulling force to a wire until it breaks or deforms. The test measures parameters such as ultimate tensile strength, yield strength, and elongation of the wire.
Pull testing provides valuable information about the wire's mechanical properties and helps assess its performance under tension. It allows manufacturers to determine if a wire can handle the expected loads and forces without failure.

Pull Testing: Evaluating Tensile Strength and Load Capacity of Wires
When it comes to assessing the quality and performance of wires, pull testing is an essential evaluation method. This test helps determine the wire's tensile strength and load capacity, making it crucial for various applications such as construction, manufacturing, and engineering. Here are some key details about pull testing:
Types of Pull Tests:
Ultimate Load Test
In this test, a wire is subjected to steadily increasing tension until it breaks. The maximum load before failure is recorded.
Yield Test
This test determines the limit at which a wire starts to deform permanently under tension. The wire is pulled until a predefined elongation is reached.
In conclusion, wire testing is crucial for ensuring the safety, quality, and performance of wires used in various industries. Pull testing is a common method to evaluate wire strength, and it is essential to follow proper procedures and standards to obtain accurate results. By conducting thorough wire testing, manufacturers can ensure that their products meet the required standards and perform reliably in their intended applications.
Torsion Test for Wire Durability
In addition to pull testing, torsion testing is an essential evaluation method for assessing the durability and performance of wires. Torsion testing involves applying twisting forces to a wire to measure its resistance to deformation and breakage. Here are some key details about torsion testing:
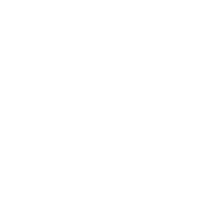
Torsion Testing: Assessing Wire Performance under Twisting Forces
In torsion testing, a wire is clamped at one end while the other end is twisted, applying torque until the wire reaches its breaking point. This test helps determine the wire's torsional strength, shear modulus, and resistance to deformation. Torsion testing is particularly important for wires used in applications where rotational forces or torsional loads are expected, such as mechanical components or electrical cables.
Overall, pull testing and torsion testing are vital methods for evaluating the strength, durability, and performance of wires. These tests provide valuable information for design optimization, quality assurance, and safety verification in various industries. By understanding these testing techniques, engineers and manufacturers can ensure the reliability and longevity of wire-based products.
Fatigue Testing for Wire Reliability
Fatigue testing is another crucial method for assessing the durability and reliability of wires under cyclic loading conditions. This test determines the wire's resistance to repeated stress cycles, simulating real-life scenarios where wires are subjected to continuous or intermittent loading. Here are some key considerations and test methods for fatigue testing:

Fatigue Testing: Evaluating Wire Endurance and Resistance to Repeated Loading
In fatigue testing, the wire sample is subjected to repeated loading and unloading cycles until failure occurs. This simulates the mechanical stress the wire may experience in real-world applications, such as in automotive, aerospace, or structural industries. The objective of fatigue testing is to evaluate the wire's endurance limit, fatigue life, and potential failure mechanisms.
Fatigue Test Methods and Interpretation of Results
There are various fatigue test methods available, including the stress-life (S-N) curve, strain-life curve, and crack initiation/propagation tests. The test method chosen depends on the specific requirements and characteristics of the wire being tested. The S-N curve, for example, plots the stress amplitude against the number of cycles to failure, providing valuable information on the wire's fatigue strength and life expectancy.
When interpreting fatigue test results, it is essential to consider factors such as the applied loads, test frequency, environmental conditions, and wire material. Reliability analysis techniques, such as statistical methods and Weibull analysis, can be used to assess the probability of failure and estimate the wire's expected life under different operating conditions.
In conclusion, torsion testing and fatigue testing are vital tools for evaluating the mechanical properties and reliability of wires. By performing these tests, manufacturers and engineers can ensure that wires meet the necessary quality and safety standards for their intended applications.
Bend Testing for Wire Flexibility
In the world of wire testing, bend testing plays a crucial role in evaluating the flexibility and strength of wires. It is essential to understand how wires bend and perform under different conditions to ensure their reliability and durability. Here, we will take a closer look at bend testing and its significance in wire characterization.
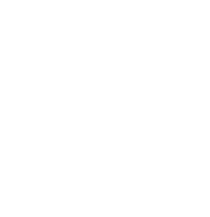
Bend Testing: Assessing Wire Flexural Strength and Performance
Bend testing involves subjecting wires to a specified radius of curvature or angle of bend. The wire is typically bent around a mandrel or a cylindrical object with a predetermined diameter. The wire is then bent multiple times, and any changes in its physical properties are observed and measured.
Procedures and Standards for Conducting Bend Testing
To ensure accurate and reliable bend testing, various procedures and standards have been established. For instance, the ASTM E290 standard outlines the test methods for bend testing of metallic materials, including wires. It specifies the equipment, test parameters, and procedures to follow for consistent and reproducible results.
During bend testing, it is crucial to carefully select the appropriate mandrel diameter and the number of bends to be applied. These parameters can vary depending on the wire's diameter, material, and intended application. The wire's performance is then evaluated based on criteria such as the number of cycles it withstands without failure or any observable damage. The significance of the radius of curvature is an essential factor to consider, as it directly influences the test's difficulty level and the evaluation of the wire's flexibility and durability.
This testing helps assess the wire's flexural strength and performance, with the general principle that the bigger the radius of curvature, the less challenging the test becomes, while a smaller radius of curvature increases the difficulty and provides a more stringent evaluation.
Elongation Test for Wire Ductility
In addition to bend testing, elongation testing is another essential test for wire characterization. This test measures a wire's ability to stretch and return to its original length, which is an indicator of its ductility or malleability.

Elongation Testing: Measuring Wire's Ability to Stretch and Return to Its Original Length
During elongation testing, a wire sample is subjected to tensile forces until it stretches to a predetermined elongation. The elongation is then measured, and the wire is released to see how well it returns to its original length. This test helps assess the wire's ability to resist permanent deformation or breakage under tension.
Importance of Elongation Testing in Wire Characterization
Elongation testing is particularly important in applications where wires are expected to undergo significant elongation during use, such as in suspension bridges or cables. It helps determine the maximum strain the wire can withstand without failure and whether it can safely accommodate the expected elongation without compromising its structural integrity.
In conclusion, bend testing and elongation testing are crucial steps in characterizing wires' flexibility, strength, and ductility. These tests help ensure that wires can withstand the rigors of their intended applications and perform reliably over time. Adhering to standardized procedures and using the appropriate test equipment is essential for accurate and consistent results.